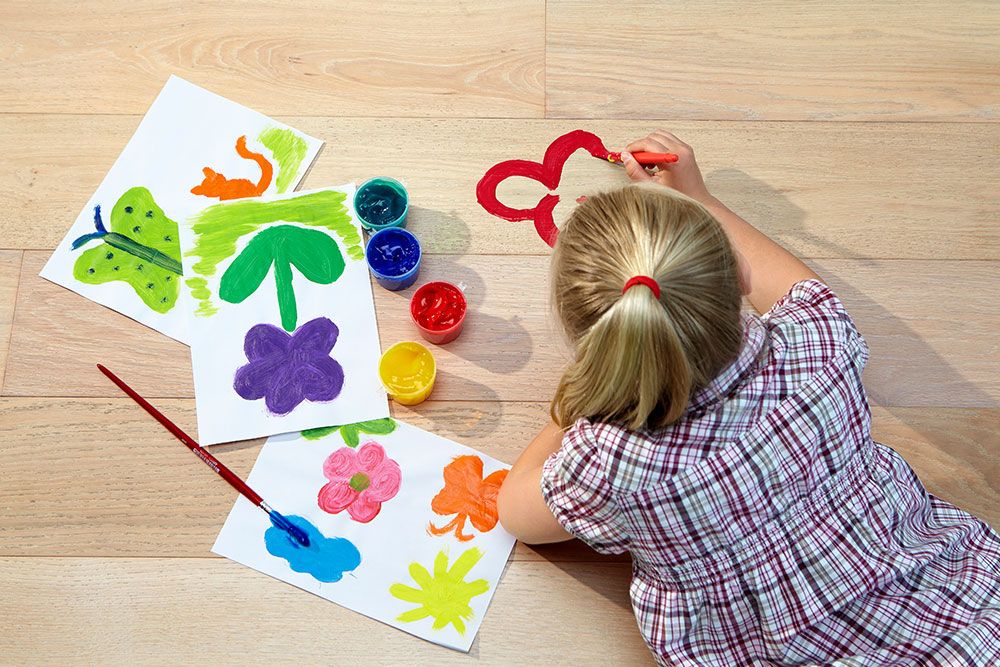
Disruption Caused by Sanding & Recoating Timber Floors
Sanding and refinishing a timber floor causes disruption, 'how much' disruption is a common question from both residential and commercial customers alike. Having floors restored can mean moving out, and in commercial applications even loss of revenue. So here we address this and other concerns to be understood.
One of the main aspects that impacts the disruption caused is healthy and safety concerns. Occupational Health and Safety guide lines are clear in this regard. Some of the chemicals and solvents used in some types of flooring industry products carry serious health risks and have a direct impact on the amount of disruption that refinishing a timber floor causes.
If they are present in the products used, the chemicals and solvents not only affect disruption but are also a compliance issue. Flooring products are now under more scrutiny from specifiers and homeowners for compliance with standards and codes, so it is important to choose wisely. Some standards (which are found on product datasheets) require products to meet limits regarding solvent content, like A+ Emissions (FR), EMICODE, DIBt & AgBB (DE) and Greenguard (US). Others like LEED, BREEAM, Living Building Challenge and GreenStar have both solvent restrictions and restrictions on the raw materials within the products together, in some cases, with other restrictions. There is also a growing movement requiring products to have an environmental product declaration (EPD) which details the environmental impact of a product or material throughout its lifecycle.
It is a flooring contractors duty to disclose what products are used, as well as their environmental and health impacts. This Duty of Care under the law extends to all people on the site during and after works, including other contractors and of course the customer or homeowner.
The key difference in disruption is the choice of either solvent based finishes or water based finishes. Solvent Based finishes carry health risks, Water Based finishes do not. If using solvent based coatings contractors are required to wear ankle to wrist PPE and breathing apparatus, and must advise others of the risk of solvent exposure & dust exposure. Peak industry body the Australian Timber Flooring Association ATFA and independent on-line sources clearly warn of these risks. Using Bona water-based polyurethane finishes do not require use of PPE, and they are compliant with or exceed all Australian Standards. When used in combination with Bona dustless sanding DCS total safety is guaranteed. Bona's DCS dust control system is rated to the highest H class accreditation which picks up 99.996% of particles 0.0003 mm in size.
The use of products containing unsafe levels of solvents presents risks to both contractors and homeowners, It has a direct affect on homeowners as the pervading solvent gases necessitate vacating the premises before reoccupation, ie the 'time before is it safe to make back in'. ATFA industry documentation (Information Sheet 91) looks in depth at the subject of offgassing which illustrates the key points:
- The escape / dispersion of volatile solvents during the drying curing phase can take days or in some cases many weeks.
- If you can still smell the solvents, then the process is still taking place, sometimes can be the case even without an odour.
- Absorbency of the substrate / number of coats – basically the more product used, the longer it takes for solvents to disperse.
- Time between coats and site conditions - If it's cold and / or there is poor ventilation the curing process takes longer.
How can Disruption be avoided when re-sanding & recoating timber floors?
Using a water based finish is the best way to minimise disruption as homeowners can stay in the house with no need to vacate premises. In commercial properties it's common for floors to be coated and the floor be put back into full commercial use 24 hours later, or sooner in some cases. If using solvent based coatings common advice is to vacate for 7 – 10 days or longer before a property can be reoccupied.
The European directive of 2007 as adopted by ATFA sets an upper limit of 140 grams / Litre VOC content for finishes. Bona's water based finishes are around 50 g/Lt with the newest products at around 30 g/Lt, less than a quarter of the EU limit. Solvent finishes contain many times this level of solvent with figures of between 300 and 800 g/Lt being common.
Years ago it was argued that solvent based products were superior in performance to water based finish systems, but this is no longer true. Bona Water based systems are the superior choice and are used on commercial floors ranging from restaurants, pubs and clubs to the Sydney Opera House and the National Portrait Gallery, shops, houses and railway station waiting rooms. The absence of health and safety risks and being able to move back in quickly makes water based finishes the obvious choice to minimise disruption when sanding and refinishing timber floors.